Trong ngành công nghiệp xi măng, lò nung clinker được ví như “trái tim” của cả dây chuyền sản xuất. Tại đây, các nguyên liệu thô được biến đổi qua phản ứng nhiệt học phức tạp để hình thành clinker – thành phần chính tạo nên xi măng Portland. Việc lựa chọn và vận hành hiệu quả lò nung không chỉ ảnh hưởng đến chất lượng xi măng mà còn quyết định chi phí năng lượng và lượng phát thải của toàn nhà máy.
1. Clinker là gì?
Clinker là sản phẩm bán hoàn thiện trong quá trình sản xuất xi măng. Nó có dạng viên nhỏ màu xám đen hoặc xám xanh, kích thước khoảng 1–25 mm, được tạo ra khi nguyên liệu thô (gồm đá vôi, đất sét, phụ gia như quặng sắt hoặc bauxite…) được nung ở nhiệt độ rất cao (1350–1450°C) trong lò quay.
Thành phần chính của clinker gồm:
Khoáng chất | Tên hóa học đầy đủ | Vai trò |
---|---|---|
C₃S (Alite) | Tricanxi silicat | Tăng độ bền sớm của xi măng |
C₂S (Belite) | Dicanxi silicat | Tăng độ bền lâu dài |
C₃A | Tricanxi aluminat | Ảnh hưởng thời gian đông kết, kỵ sunfat |
C₄AF | Canxi aluminoferrit | Tạo màu xi măng, ít ảnh hưởng cơ lý |
Sau khi có clinker, người ta nghiền nó cùng với thạch cao (để điều chỉnh thời gian đông kết) và phụ gia khác → tạo thành xi măng thành phẩm.
2. Lò nung clinker hoạt động thế nào?
Cấu tạo và cơ chế hoạt động
Lò nung clinker là một ống quay bằng thép, hình trụ, được đặt nghiêng từ 3–4 độ so với mặt phẳng nằm ngang. Chiều dài lò khoảng 50–80 mét, đường kính 3–6 mét. Vỏ lò được lót gạch chịu lửa để bảo vệ khỏi nhiệt độ cao và sự mài mòn.
Lò được quay với tốc độ chậm (khoảng 0.5 – 5 vòng/phút) nhờ hệ thống gối đỡ và bánh răng truyền động. Nguyên liệu đầu vào (bột liệu) được đưa vào từ đầu cao của lò, di chuyển dần xuống đầu thấp dưới tác động của trọng lực và chuyển động quay.
Quá trình trao đổi nhiệt và phản ứng
Nguyên liệu trong lò trải qua ba vùng nhiệt chính:
- Vùng sấy (100–600°C): Nước ẩm bay hơi
- Vùng tiền nung (600–900°C): CaCO₃ phân hủy thành CaO và CO₂
- Vùng nung kết (1200–1450°C): Các oxit phản ứng để hình thành clinker
Nguồn nhiệt được cung cấp từ đầu thấp của lò thông qua hệ thống đầu đốt (burner) sử dụng nhiên liệu như than đá, khí tự nhiên hoặc nhiên liệu thay thế (RDF). Không khí cấp từ quạt gió giúp duy trì quá trình cháy ổn định. Khí nóng di chuyển ngược chiều với nguyên liệu (từ đầu thấp lên đầu cao), tạo hiệu ứng trao đổi nhiệt hiệu quả.
Sản phẩm đầu ra
Sau khi hoàn tất quá trình nung kết, clinker được đẩy ra khỏi lò và rơi xuống hệ thống làm mát (cooler), sau đó chuyển tiếp đến kho chứa để nghiền thành xi măng.
Kiểm soát vận hành
Lò nung hiện đại được giám sát bằng hệ thống điều khiển tự động (PLC/DCS), cảm biến nhiệt hồng ngoại, đo áp suất và lưu lượng khí để đảm bảo quá trình diễn ra chính xác, liên tục và an toàn.
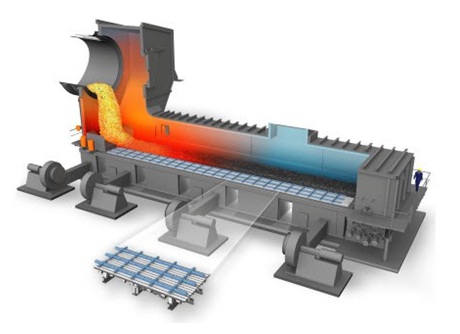
4. Ưu điểm công nghệ lò quay nung clinker hiện đại
Công nghệ lò quay nung clinker hiện đại không chỉ nâng cao năng suất và chất lượng sản phẩm, mà còn đáp ứng yêu cầu về môi trường, tự động hóa và tiết kiệm năng lượng – là lựa chọn tất yếu cho các nhà máy xi măng hiện đại hóa dây chuyền.
Hiệu suất nhiệt cao, tiết kiệm nhiên liệu
Công nghệ lò quay khô hiện đại tích hợp hệ thống trao đổi nhiệt đa cấp (cyclone preheater) và buồng tiền nung (calciner) giúp tận dụng triệt để nhiệt từ khí thải, làm nóng sơ bộ và khử cacbonat nguyên liệu trước khi vào lò chính. Nhờ đó:
- Mức tiêu thụ nhiệt giảm còn < 800 kcal/kg clinker
- So với lò ướt, tiết kiệm đến 30–40% lượng nhiên liệu đốt
Kiểm soát chất lượng clinker chính xác
Lò hiện đại sử dụng các thiết bị giám sát như:
- Cảm biến nhiệt IR để theo dõi nhiệt độ dọc thân lò
- Hệ thống điều khiển tự động PLC/DCS, cho phép điều chỉnh tốc độ quay, lượng liệu, nhiên liệu và lưu lượng gió tức thời → Giúp clinker đầu ra có thành phần khoáng pha ổn định, hạn chế clinker sống hoặc quá nung.
Khả năng vận hành linh hoạt, tự động hóa cao
- Có thể điều chỉnh năng suất theo nhu cầu (từ 3000 đến 10000 tấn/ngày)
- Tự động khởi động, dừng lò, cảnh báo sự cố
- Dễ tích hợp với hệ thống SCADA hoặc hệ thống quản lý sản xuất tổng thể (MES)
Giảm thiểu phát thải và thân thiện với môi trường
- Giảm lượng khí CO₂ phát sinh nhờ:
- Giảm tiêu hao than
- Đồng đốt với nhiên liệu thay thế như RDF, biomass
- Khí thải được xử lý qua lọc bụi túi vải (bag filter), hoặc lọc tĩnh điện (ESP), đảm bảo đạt chuẩn môi trường
- Có thể tích hợp hệ thống thu hồi nhiệt để phát điện (WHR)
Tuổi thọ cao, bảo trì thuận tiện
- Kết cấu lò được tính toán chịu mỏi và mài mòn
- Gạch chịu lửa thế hệ mới tăng tuổi thọ vùng nung
- Dễ bảo trì nhờ thiết kế modul hóa các bộ phận (burner, gối đỡ, quạt, motor)
Dễ tích hợp số hóa và công nghệ mới
- Sẵn sàng chuyển đổi sang các dạng nhiên liệu thay thế, thậm chí hydrogen trong tương lai
- Có thể áp dụng AI để dự đoán hư hỏng, tối ưu quá trình nung
- Dễ kết nối với hệ thống quản lý sản xuất thông minh
Tích hợp môi trường và hiệu quả năng lượng
Nhiều nhà máy xi măng hiện nay đang hướng đến:
- Tận dụng nhiệt thải để phát điện (WHR – Waste Heat Recovery)
- Đồng xử lý chất thải công nghiệp trong lò nung
- Áp dụng IoT/AI để theo dõi tình trạng thiết bị và tối ưu năng lượng
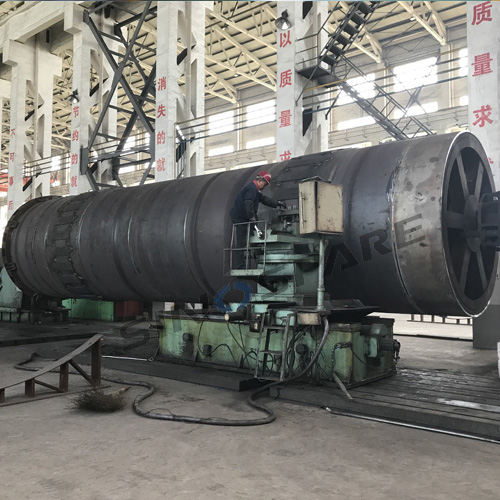
5. So sánh lò quay khô và lò ướt
Tiêu chí | Lò quay khô | Lò quay ướt |
---|---|---|
Nhiệt độ nung | 1350 – 1450°C | 1400 – 1500°C |
Nhiên liệu tiêu thụ | Thấp (800 – 1000 kcal/kg) | Cao hơn (1300 – 1500 kcal/kg) |
Chất lượng clinker | Ổn định, dễ kiểm soát | Dễ bị dư ẩm nếu vận hành sai |
Mức độ cơ giới hóa | Cao, tự động hóa | Trung bình |
Ứng dụng hiện nay | Chủ yếu dùng phổ biến | Giảm dần, ít còn sử dụng |
6. Xu hướng công nghệ lò nung clinker trong tương lai
Trước áp lực toàn cầu về giảm phát thải khí nhà kính và yêu cầu nâng cao hiệu quả sản xuất, công nghệ lò nung clinker đang chuyển mình mạnh mẽ theo các hướng sau:
Tối ưu hóa tiêu hao năng lượng
Các hãng công nghệ đang phát triển lò siêu dài kết hợp preheater và calciner nhiều tầng, giúp tận dụng triệt để nhiệt khí thải. Một số mô hình thử nghiệm ghi nhận mức tiêu hao chỉ < 700 kcal/kg clinker, thấp hơn 15–20% so với các lò hiện nay.
Chuyển đổi sang nhiên liệu sạch
- Hydrogen đang được nghiên cứu như giải pháp thay thế than trong lò nung, với ưu điểm không phát thải CO₂.
- RDF, biomass, dầu thải tiếp tục là nhiên liệu thay thế phổ biến do chi phí thấp và khả năng đồng xử lý chất thải.
Tích hợp công nghệ số – trí tuệ nhân tạo
- AI + IoT được ứng dụng để dự đoán hỏng hóc, tối ưu nhiệt độ, tốc độ quay và lưu lượng khí.
- Hệ thống digital twin (bản sao số) mô phỏng toàn bộ quá trình vận hành giúp kỹ sư thử nghiệm các kịch bản mà không cần can thiệp trực tiếp vào lò thật.
Tích hợp công nghệ thu hồi và lưu giữ CO₂ (CCS
Trong tương lai gần, các lò nung clinker sẽ tích hợp thêm:
- Thiết bị tách CO₂ sau đốt, thu gom khí thải để xử lý hoặc tái sử dụng
- Công nghệ oxy-fuel combustion, đốt bằng oxy tinh khiết để dễ thu CO₂ hơn → Hướng đến nhà máy xi măng không phát thải (net-zero cement plant)
Mô hình hóa và thiết kế lò nung theo dữ liệu lớn
Thiết kế lò nung mới sẽ sử dụng mô phỏng CFD (Computational Fluid Dynamics), dữ liệu thời gian thực, và tối ưu hình học để đảm bảo:
- Nhiệt phân bố đều
- Giảm vùng “chết nhiệt”
- Tăng tuổi thọ gạch chịu lửa
Tương lai của công nghệ lò nung clinker sẽ không chỉ nằm ở việc tối ưu hiệu suất mà còn là sự hòa quyện giữa cơ khí, số hóa và bền vững môi trường. Những nhà máy xi măng tiên phong trong việc chuyển đổi sang mô hình “carbon thấp” và tích hợp công nghệ AI sẽ là những người dẫn đầu thị trường trong giai đoạn tới.
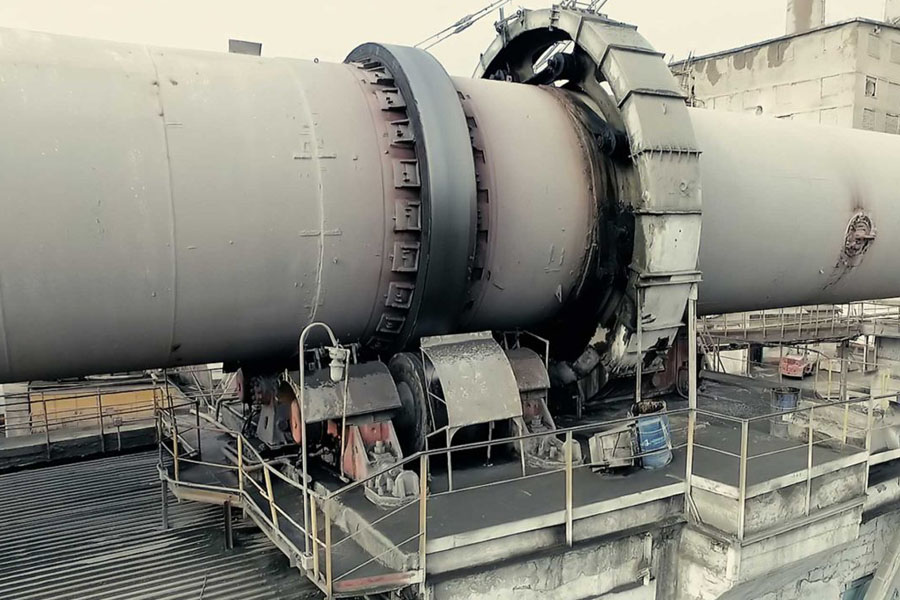
Lò nung clinker đóng vai trò then chốt trong sản xuất xi măng. Một hệ thống lò hiện đại, tối ưu hóa vận hành và thân thiện môi trường sẽ giúp doanh nghiệp giảm chi phí, nâng cao chất lượng sản phẩm và đáp ứng tiêu chuẩn bền vững toàn cầu. Nếu bạn là doanh nghiệp đang tìm kiếm giải pháp đầu tư – nâng cấp dây chuyền sản xuất, thì việc lựa chọn đúng công nghệ lò quay clinker hiệu suất cao chính là bước đi chiến lược quyết định trong lộ trình phát triển bền vững.
SINOVINA – với nhiều năm kinh nghiệm trong lĩnh vực cung cấp giải pháp thiết bị và công nghệ ngành xi măng – cam kết đồng hành cùng các nhà máy trong việc:
- Tư vấn, thiết kế và cung cấp lò nung clinker theo yêu cầu thực tế
- Tích hợp công nghệ tiết kiệm năng lượng, giảm phát thải
- Hỗ trợ vận hành và bảo trì sau lắp đặt
Liên hệ với SINOVINA ngay hôm nay để được tư vấn giải pháp lò nung clinker phù hợp nhất cho dây chuyền sản xuất của bạn – hiện đại, hiệu quả và sẵn sàng cho tương lai.